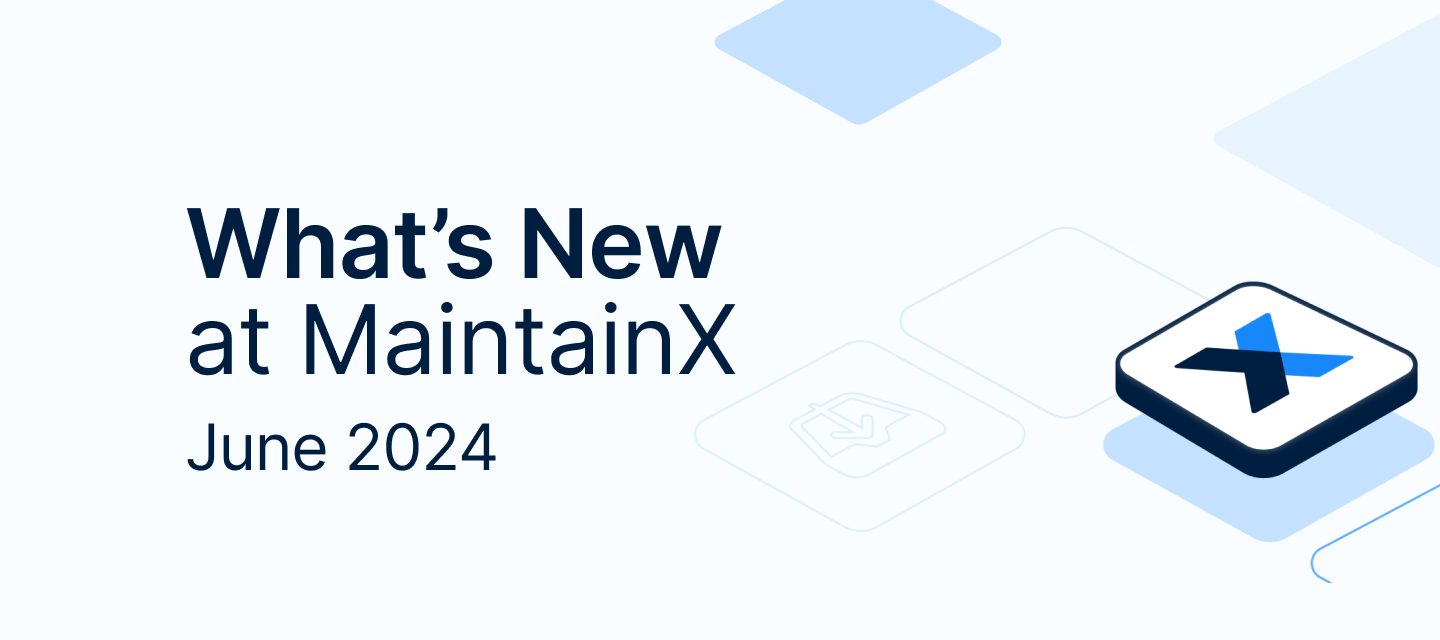
What’s New at MaintainX: June 2024
As summer kicks into gear, MaintainX has doubled down on AI-driven innovation and integrations to drive operational efficiency for customers.Last week, we released a bundle of new AI-powered functionality to optimize and streamline daily workflows and decision-making.Smart Time Estimates, one of several improvements to MaintainX’s Resource Planning module, helps you schedule work more efficiently using AI to estimate how long work orders will take to complete. We’ve also expanded Anomaly Detection to work with non-recurring work orders and manual meter readings, to minimize human error and detect early signs of equipment failure.And, if that wasn’t enough to help you get more from your data, we’re also proud to have launched our new Integrations Marketplace. With a selection of pre-built and custom integrations, expert-led services, and an open API, it’s easier than ever to connect MaintainX with your ERP, IoT devices, SCADAs, Historians, and other software.Let’s take a closer look at what’s landed in the past month—and how you can use these new features to increase your production capacity and reduce costs.Make your daily workflows and decisions smarter with AI There’s a reason why the AI market for industrial machinery is set to grow by $5.46bn over the next four years. Many companies have collected a mountain of data, enabling AI to become a force multiplier for positive business outcomes.But despite the huge opportunities presented by AI, most organizations aren’t using it yet to streamline their day-to-day operations.To help you put AI to work in a fast, focused way, MaintainX customers on the Enterprise plan can now use AI-powered Smart Time Estimates to plan and schedule tasks. Smart Time Estimates uses historical data and AI to create an informed estimate on how long a new work order should take to complete – improving planning flexibility, efficiency, and accuracy.Along with our Resource Planning module, which allows you to balance workload quickly across your team, Smart Time Estimates goes even further to maximize productivity, reduce overtime, and enable you to get more done on time.AI-powered time estimates will automatically populate the Estimated Time field in your work orders, and the accuracy will continue to improve as you collect more data. Our expanded Anomaly Detection technology, also available on the Enterprise plan, now works on non-recurring work orders and in the manual readings from the Meters module.When a technician enters a value that deviates from the expected range, based on previous inputs, they’ll be asked to check it. If they confirm that the value is an anomaly, they’ll be prompted to create a corrective action to ensure that any potential equipment faults are addressed.By extending this feature beyond recurring work orders, anomalies can be flagged on specific meters or equipment that’s not necessarily subject to regular inspections. This does even more to protect you against costly reactive work.Connect and standardize your data with the Integrations Marketplace Driving operational excellence requires collaboration across your facility, from maintenance and operations, to finance and management.Integrating the systems your teams rely on is crucial for seamless data flow and empowered decision-making. That's why we're excited to introduce the MaintainX Integrations Marketplace — a central hub to find available integrations and information on how to get started.By connecting MaintainX with your operational technology, ERP, business intelligence tools and more, you can simplify workflows, synchronize data, and unlock new insights. Maintenance technicians, finance teams, and managers can work from the same reliable data, and make informed decisions that drive efficiency and reduce costs. To make integrations straightforward and accessible, we offer three options to meet your needs:Expert integration services: MaintainX provides integration services through our agile in-house team that handles all the coding for you. Skilled systems integrators (SIs): We can connect you with experienced SIs who will ensure the effective execution of your integration projects. Do it yourself: For those who prefer a hands-on approach, you can leverage our comprehensive API Documentation or Zapier—a low-code platform that connects MaintainX with hundreds of other applications.For more information, visit our Integrations Marketplace.Schedule work more easily with Resource Planning improvements In addition to Smart Time Estimates, we also made several improvements to MaintainX’s Workload View to help teams balance workloads, maximize wrench time, and keep everyone on the same page. These updates include:Multiple Day WOs: Schedule Work Orders in the Workload View and drag them across multiple days. Reschedule Incomplete Work Orders: Keep track of missed work by reviewing and rescheduling incomplete past Work Orders Control Panel View: For team members with multiple jobs, quickly view and adjust their workload in one panel view. Weekly View On Mobile: Give your team a weekly view of their workload on the go Start Date Not Limited By Due Date: Allow for flexible rescheduling by allowing start dates to be after their due date.Resource Planning is available on the Enterprise Plan.Other improvements fueled by customer feedbackAs always, there were many other smaller improvements delivered to MaintainX customers over the past month.Work Order fields can now be marked required in your Organization settings, by navigating to Features > Work Orders > Set Preferences > Customize Work Order Form > Required Fields. Making fields mandatory helps to improve your data quality by ensuring inputs aren’t skipped.And to help serve our global customer base, we also translated some of our MaintainX Academy courses into Spanish. Introduction to MaintainX, Administrator Foundations and Technician Foundations can all now be accessed in Spanish to help managers and technicians get up to speed with MaintainX.We thank our customers for continuing to provide such great feedback. It helps us to grow, innovate, and improve MaintainX more every month—which helps organizations like yours to become smarter and more efficient.If you’re not yet a MaintainX customer, book a tour today.